Surveys showed that this product category had some unmet interest. It’s an old concept from the 90’s and although there was some competition none really worked very well. The point of the product is that you put it on your half-finished soda bottle, “Pump It Up” with air to high pressure, and that keeps it carbonated longer. Here’s some of the other products on the market:
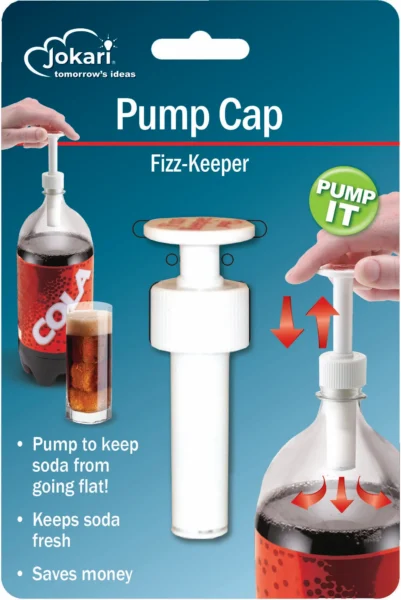
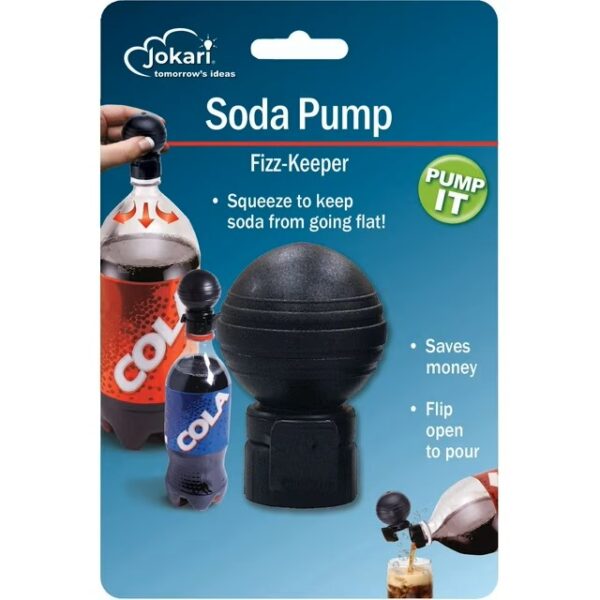
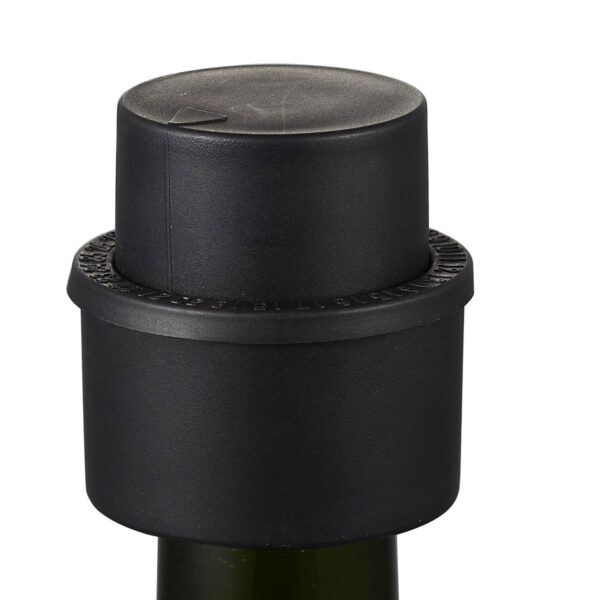
First Principles Research
The first thing I did was start researching whether this product is actually effective. My intuition said that it would help but would never be perfect. The products claim to keep your drinks carbonated longer. Reviews are generally excellent. On the other hand, a lot of articles argue that it doesn’t work based on theory. Here’s my understanding.
For the carbonation to be stable, the system must have the same rate of CO2 dissolving into the water as is dissolving into the headspace of the bottle. In an unopened bottle, the headspace is 100% CO2, typically around 30 psi. Essentially, the headspace is pushing CO2 into the water just as hard as the water is pushing it out. Normal air is only 0.04% CO2, so after a bottle is opened and reclosed, CO2 will diffuse out of the water more than it diffuses into the air until it reaches a new equilibrium. Even if you were to pump the bottle back up to 30 PSI with air, it would still not have nearly enough density of CO2 in the headspace to be stable. Other molecules in the air don’t have an effect on the equilibrium of CO2, a fact that is somehow both unintuitive and obvious at the same time. You would have to pump it up to about 75,000 PSI before the density of CO2 in the headspace was equivalent to that of a fresh bottle. But there’s a twist! The literature does say that increasing the pressure slows down the loss of carbonation. The extra density of the air makes the CO2 molecules diffuse slower. How strong that effect is was not easily found in the literature.
I decided to test it myself. I set up a blind taste test with my co-workers comparing a half-opened bottle closed with the Fizz Keeper to a bottle closed with the standard cap. I also made a bottle cap to a bike pump adapter so that I could pressurize a bottle up to a known pressure. Fizz Keeper did come out with a slight lead, but it was not a very big effect and you can see results are not very consistent person to person so there is lot of noise in this data.
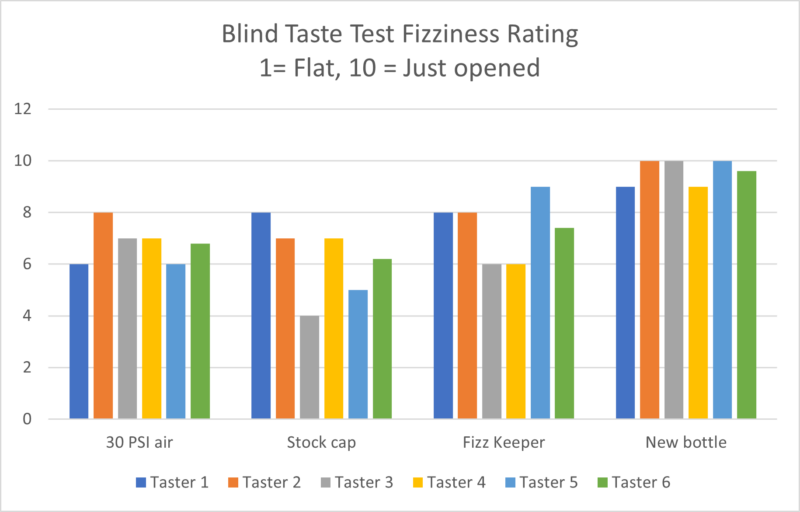
I next tried to come up with something more quantitative. If only you could capture the CO2 coming out of the soda. I pumped one bottle up to using the Fizz Keeper. The other I just opened, emptied to the same level, and closed with the standard cap. After 24 hours I took both caps off, releasing the headspace air, then put balloons on top of the bottles and lightly swirled the bottles until they stopped off-gassing. To my surprise, the bike-pumped soda actually did have more air! It’s not much, but it’s not nothing either.
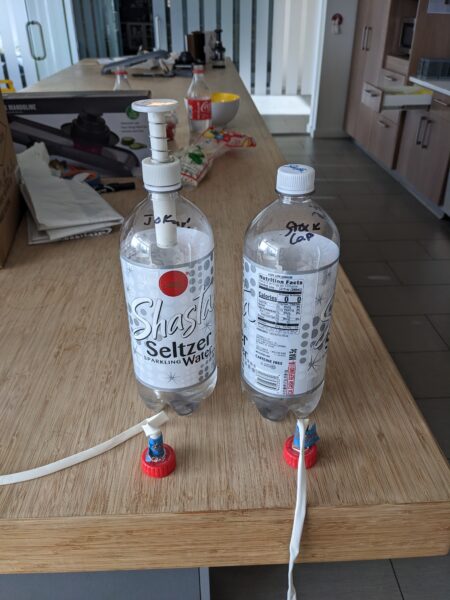
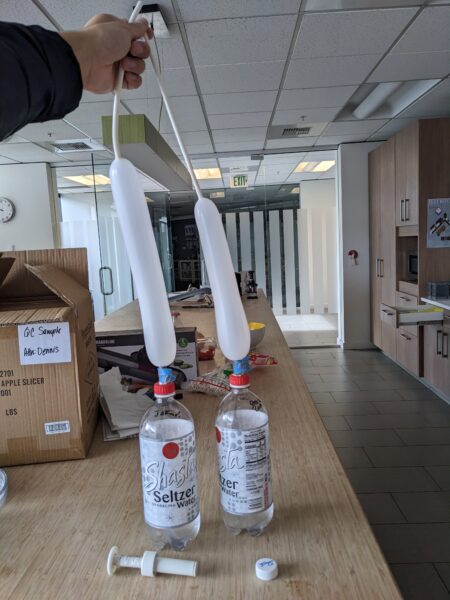
Design
The Fizz Keeper is still on the market and it hasn’t changed in 25 years. The main thing we wanted to improve was the valves. The Fizz Keeper will frequently not work on some strokes. It eventually will get up to pressure, but you can feel that the valves aren’t consistently working sometimes. The other thing was that it does take a while to pump up, especially on a larger 2L bottle. To help with this, we added a spring so the user can just slap it quickly, rather than pulling it up and down. This would make the bottle too tall for any normal fridge shelf though, so we added a bayonet lock to keep the plunger down.
We explored some alternative formats but decided to maintain the integrated pump format. The item is basically a spring-loaded piston with two check valves. I designed a small silicone umbrella valve for the inlet and outlet. In some competitor’s products, each check valve is made of two parts, sometimes with a metal spring, so this part reduction saved some money to offset the added piston spring. For the sealing between the head and they cylinder I used a skirt shaped gasket overmolded to the piston head. It’s designed to have some self-help. On the downstroke, air pressure pushes the skirt out to increase the sealing strength. On the upstroke, it can easily collapse so it doesn’t fight the spring too much. I crunched some numbers to figure out the compression ratio needed to generate enough pressure and ensured there would be enough space for the valve and the spring. It had to have a conical spring so that it could be flattened as much as possible, maximizing the compression ratio.
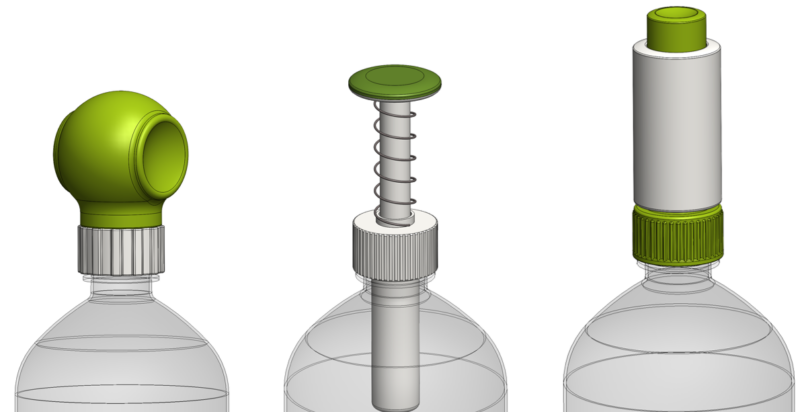
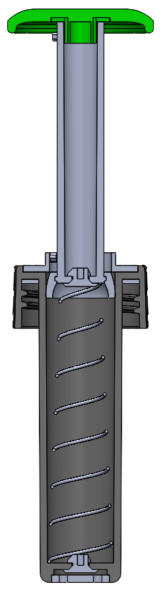
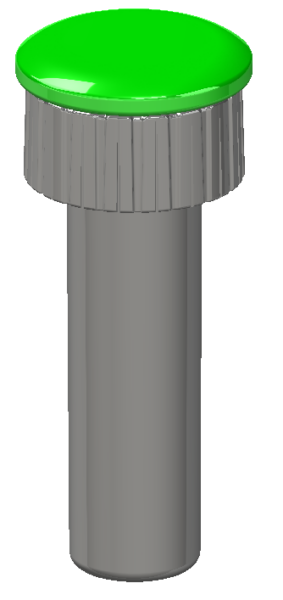
During off-tool testing, we dealt with some issues. Airtight testing was slow. You can check for a fast air leak by submerging the item, but it takes multiple days to test a very slow leak. Both of the valves and the gasket took a few T-cycles to get right.
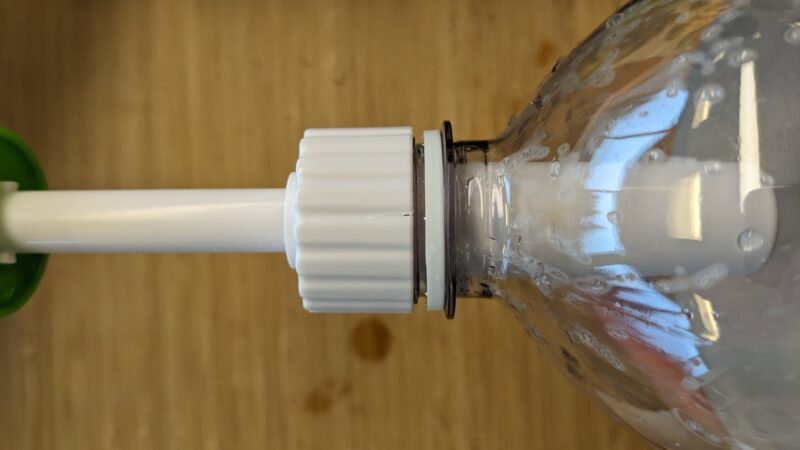
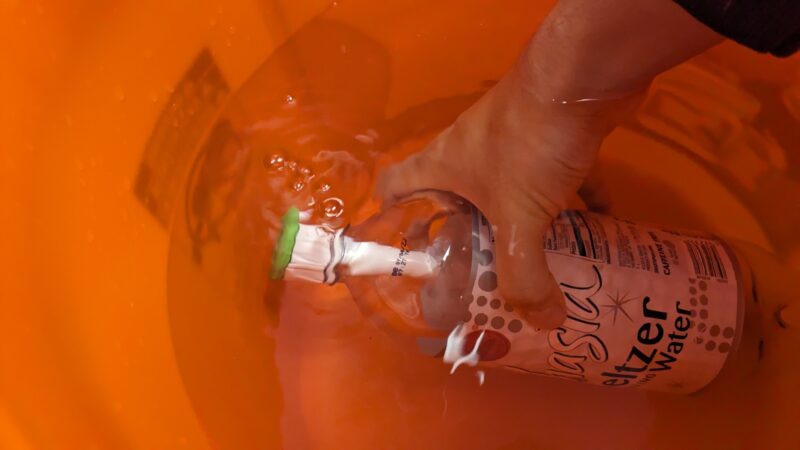
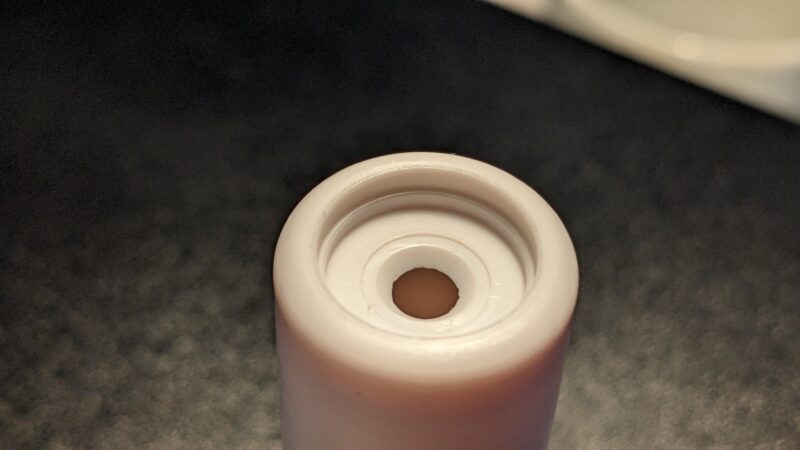
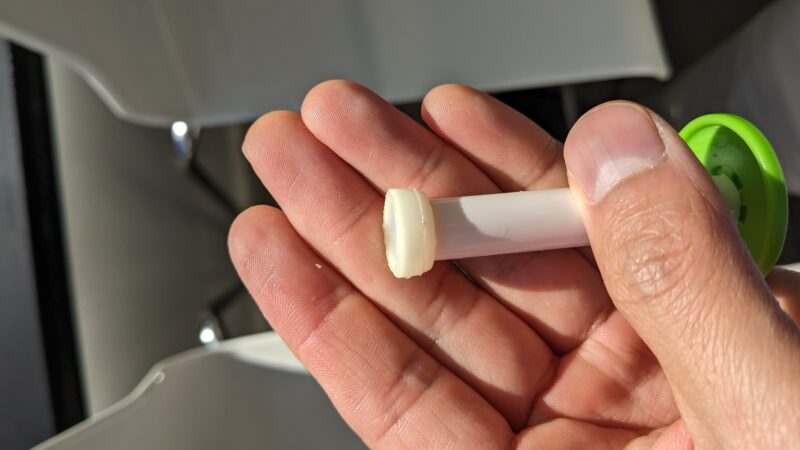
Conclusion
In the end, the item launched in 2024 and was well received by buyers. For me it was a rewarding project because it grew my knowledge in realms like pneumatics and chemistry which I don’t often use in the kitchen gadget world.
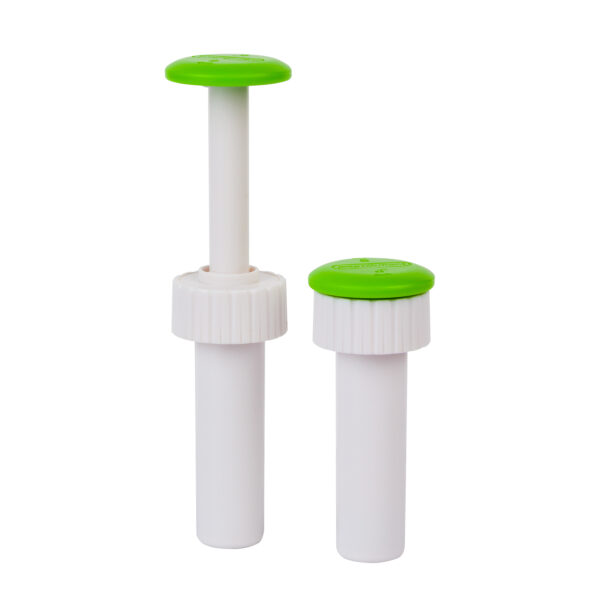
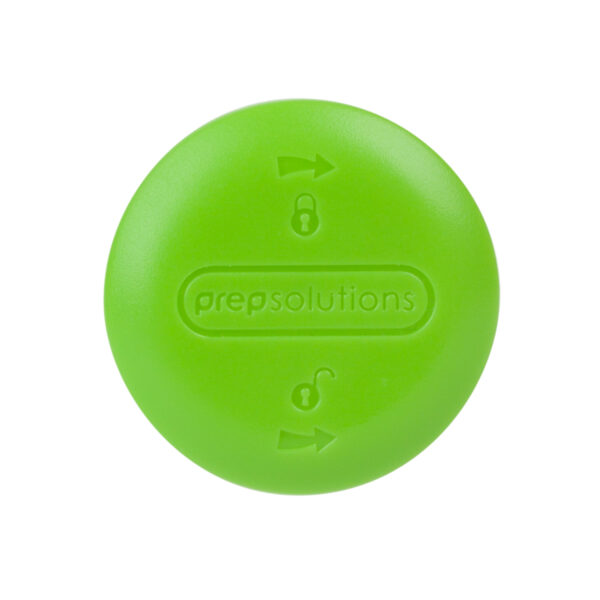
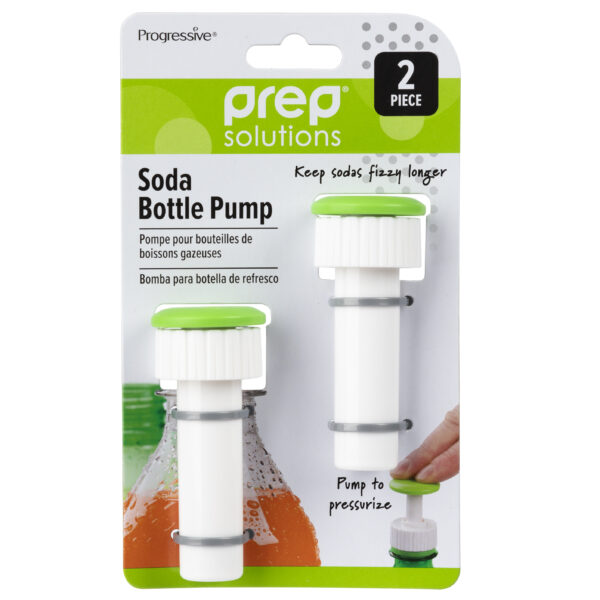